ARGONAUT - Efficient and resource-saving production of aviation transmissions
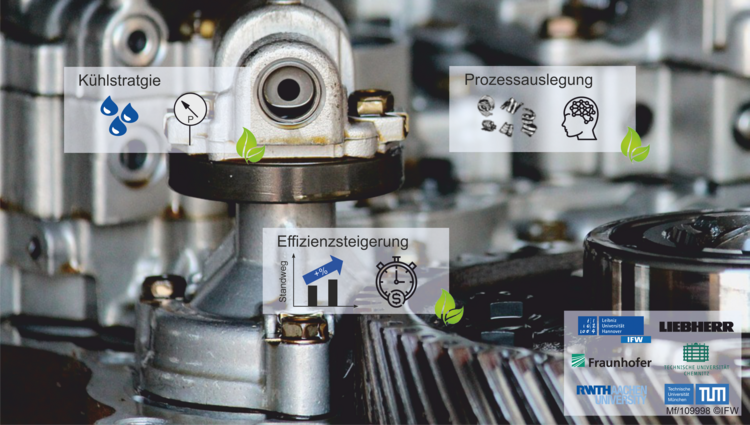
Led by: | Prof. Dr.-Ing. Berend Denkena |
E-Mail: | murrenhoff@ifw.uni-hannover.de |
Team: | Marita Murrenhoff (IFW Hannover), Felix Zender (IFW Hannover), RWTH Aachen, Fraunhofer-Gesellschaft, TU München, TU Chemnitz |
Year: | 2022 |
Date: | 04-07-22 |
Funding: | BMWK |
Duration: | 01/2022 – 03/2025 |
In this research project funded by the BMWK, the IFW is investigating the demand-oriented use of cooling lubricant in the first subproject. This offers great potential for increasing resource efficiency in machining, since many processes are carried out with the maximum available coolant pressure, even though this would not be necessary due to the respective meshing conditions. Especially since the required coolant pump is one of the main consumers of the machine tool, considerable savings potentials result from an adapted control of the coolant pressure. Accordingly, knowledge about the adapted cooling lubrication strategies will be developed within the scope of the research project. In addition, a CAD/CAM-controlled NC code planning system will be developed to adapt the coolant pressure to the respective cutting conditions.
In addition to geometrically determined cutting, new developments in the field of geometrically indeterminate cutting also offer potential for increasing performance in interaction with the use of cooling lubricant. Due to the large contact areas and geometric dimensions, internal grinding processes are considered challenging in terms of process stability and the risk of surface damage due to grinding burn. One possibility to better supply the hard-to-reach contact zone with cooling lubricant is the use of additively manufactured grinding wheels. Here, on the one hand, the microstructuring of the surface offers the potential to produce a cooler grind. In addition, additive technology can also be used to produce grinding wheels with internal cooling channels, allowing the cooling lubricant to reach the contact surface between the workpiece and the tool directly.
In the second subproject, knowledge of process optimization and automation through improved chip breaking and the use of novel, innovative turning processes will be developed at IFW. The high potential of chip breakage control by means of process-adapted chip guidance geometries is to be applied in the production of gear components. Typically, aerospace materials are long-chipping materials. Long strip or swirl chips cause damage to the workpiece surface, reduce tool life and hinder automated processes. Therefore, the aim of the three-year research project is to achieve an increase in process reliability by improving chip breaking behavior, thus creating the prerequisite for the automation of complex turning processes. First of all, indexable inserts available on the market with chip-guiding geometry will be investigated. Subsequently, new chip grooves are developed with the aid of simulative methods and applied to inserts by means of laser ablation. Furthermore, complex turning processes with additional axis movements are investigated in order to increase productivity and process reliability in the machining of aerospace components. Due to the time-variable chip shape, the analysis of chip breaking behavior is particularly challenging in these processes. By means of material removal simulation, detailed investigations of the influence of the chip shape on the chip breaking behavior are to be carried out. The aim is to achieve a favorable chip shape in the complex turning processes by means of adapted process control.
Finally, the knowledge gained will be integrated in the Liebherr company's real production environment, both for the adapted cooling lubrication strategy and for the increased chip breaking behavior.